Ensure safety with TEAL’s EV battery pack assembly solutions
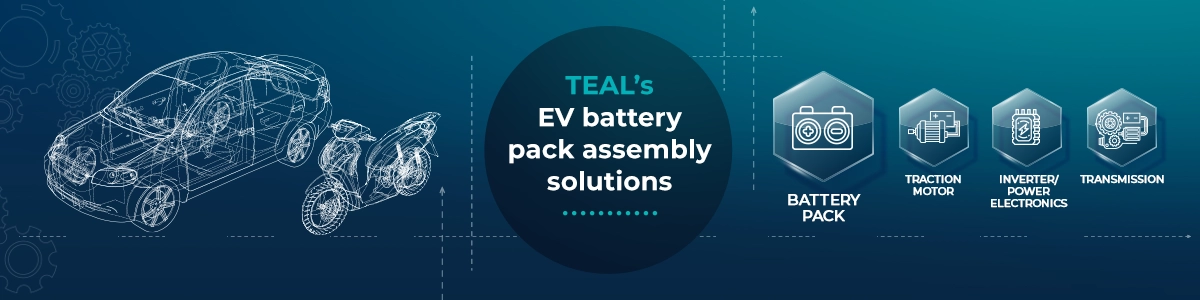
Electric vehicles (EVs) are becoming an increasingly popular alternative to traditional petrol and diesel cars, as consumers become more aware of the environmental impact of vehicles. With climate change and global warming high on the agenda, people are looking for ways to reduce their carbon footprint and improve air quality. Switching to an electric car is one of the quickest and most effective ways to do this. EVs produce zero emissions, which helps to reduce pollution and improve air quality. With more and more people making the switch to EVs, we can expect to see a significant reduction in greenhouse gas emissions from the transport sector.
The industry automation solutions has begun to shift from conventional forms of mobility, like internal combustion engines (ICE), to EVs because of climate change and resource shortages. EVs are not only more environmentally friendly, but they are also more efficient in terms of resource use. This switch will not only benefit consumers but will also help the automotive industry to meet its sustainability goals.
The adoption of EVs is on the rise
The recent push for EVs in India has created a wealth of business opportunities in three key areas: mobility, infrastructure, and energy. These include opportunities in the EV OEM market, EV battery pack assembly, battery infrastructure, EV franchising, solar vehicle charging, and battery swapping technology, to name a few.
The electric vehicles (EVs) market is expected to be worth at least INR 475 billion by 2025, according to a recent study. The Indian automobile industry is one of the largest in the world and is projected to become even larger in the coming years. By 2030, it is expected to be the third-largest automotive market in the world. This growth is being fueled by the expansion of the electric vehicle (EV) market in India, which is expected to grow at a compound annual growth rate (CAGR) of 36% according to the India Energy Storage Alliance (IESA). With the population continuing to grow and the demand for vehicles increasing, India cannot sustain its current level of dependence on imported crude oil. Making the switch to EVs is crucial in order to reduce environmental pollution and reliance on fossil fuels. This is aligned with the goal of achieving net zero carbon emissions by 2070. In the last three years, there have been 0.52 million EVs registered in India, according to the Ministry of Heavy Industries. EV growth has been strong in 2021 due to supportive government policies and programs.
The electric vehicle industry in India is slowly starting to pick up speed, with support from government initiatives and increased demand for alternatives to traditional petrol and diesel cars as people look for ways to reduce their monthly expenses. However, a widespread switch from internal combustion engine (ICE) vehicles to EVs will require an expansion of infrastructure facilities, including charging stations, efficient EV battery pack assembly, and vehicles that can travel a greater distance on a single charge.
The government has set an ambitious target of 100% electric vehicles (EVs) on roads by 2030. Given the current state of the country’s manufacturing and adoption of EVs, this target appears to be achievable with several initiatives taken by the government to support the industry.
It’s crucial to understand safety concerns & country regulations for EVs
As electric vehicles (EVs) become more popular, questions about their safety are increasing. Let’s take a look at how the government is concerned about the safety and has initiated regulations for EVs. In an effort to meet its target of installing 450 GW of renewable energy by 2030, India has placed renewed focus on clean mobility through increased penetration of electric vehicles. The road transport ministry has put together a panel of experts to come up with additional safety requirements which are due by 1 December 2022. To ensure safe e-mobility, the government has drafted another set of EV battery safety norms, Phase II, which will come into effect on 31 March 2023. The aim is to have all vehicles plying on Indian roads meet these standards so as to avoid any accidents or mishaps that might occur due to faulty batteries.
In an effort to reduce its overall carbon footprint, India has set an ambitious target of electrifying 70% of all commercial cars, 30% of private cars, 40% of buses, and 80% of two- and three-wheelers by 2030. This shift is also in line with changing customer preferences, with surveys suggesting that 66% of Indian consumers are now more inclined to purchase electric vehicles or prefer using them for commuting. An important factor in order for a country to rapidly adopt clean and green mobility is to have a firm focus on creating a dependable EV charging infrastructure. Another measure that must be taken is the utilization of innovative technologies to make batteries more durable and reliable. Therefore, the government’s decision to take additional steps to improve battery standards is a great opportunity for both manufacturers and customers.
A few key players that can unlock capital for electric vehicles are OEMs, private banks, NFBCs, fleet operators, startups, and fintech companies. The country has made significant but gradual progress in the growth of the EV ecosystem, which has encouraged the state and central governments to reform EV policies and incentivize the domestic manufacturing of charging infrastructure, EVs, and batteries.
The government’s recent decision to increase its focus on electric vehicles comes at a time when there have been several reports of such vehicles catching fire in different parts of the country. The amendment process includes important safety requirements like battery cells, a battery management system, an onboard charger, and a design for the battery pack that takes into account thermal propagation due to an internal cell short circuit, which could lead to a fire. The recent reports of fire incidents have led the government to take a closer look at testing criteria and standards, as well as the reasons for fires. The government has issued guidelines to improve the connection of EV battery cells and the venting mechanism to disperse heat in case of overheating. These improvements are expected to make the EV ecosystem in India more advanced and safe.
Customer requirement for automation is increasing day by day
The government's support for EVs has led to an increase in demand for faster EV production, which has in turn caused the sector to embrace automation. There are several reasons for this, including the growing complexity of the manufacturing process, the need for greater flexibility and responsiveness to customer demand, and the fast-paced nature of business. As a result, manufacturers are under pressure to produce products faster and with higher precision to ensure safety. To meet this customer demand, manufacturers must be able to automate their processes in order to support the market requirement in a short time.
Automation is a critical aspect for manufacturers looking to efficiently produce high-quality products that meet customer specifications. By implementing automation systems , manufacturers can improve product quality and consistency, as well as decrease manufacturing costs. As the market shifts, automation becomes an increasingly appealing option for manufacturers. However, the specific automation needs for building battery packs depend on the size, shape, and type of battery cells being used, such as cylindrical cells, prismatic cells, pouch cells, and blade cells.
TEAL: A reliable partner for your automation and EV battery pack assembly needs
With the invention of the lithium-ion battery, electric vehicles (EVs) are becoming increasingly popular as a more sustainable option. At Titan Engineering and Automation Limited (TEAL), we offer efficient and precise EV battery pack testing assembly , giving our customers a competitive edge in a rapidly changing market. In order to keep up with the market requirements, we offer a battery pack automation in assembly line that is modular in design. This offers our customers a number of benefits, including flexibility, adaptability, standardization, and maintainability. It makes it easy for our customers to ramp up production volume when needed.
As transportation continues to electrify, advancements in safety, energy density, and cost-effectiveness are making it possible on a large scale. This shift is opening up new design possibilities that were once unthinkable. Robust EV battery pack assembly solutions are what’s needed in order to make these applications a reality. Here at our company, we have extensive expertise in the field of turnkey assembly and testing automation solutions. Moreover, our experience in diversified industry segments allows us to offer solutions for even the most challenging applications out there. And, as an added bonus, we customize all of our solutions to fit the specific requirements of each individual customer.
When you are ready to take your product from prototype to mass manufacturing, you can count on us to do it right the first time. We have the experience and expertise to make sure your product is made to the highest standards, so you can focus on other aspects of your business.
Learn how TEAL can help you streamline your EV battery manufacturing process
EV battery pack calls for the highest standard for assembly considering safety. TEAL jointly works with the customers even during the development stages to ensure the best-of-its-kind solution that is customized as per their requirements.
We have developed the automatic battery pack ev battery assembly that includes battery cell sorting, cleaning, dispensing, welding, dispensing, tightening, leak testing, etc. that ensures the assembly requirement of our customers. By using this automated ev battery technology , our team guarantees that each EV battery pack meets the highest standards before it leaves the factory floor. There is a need for traceability in today’s world, and TEAL offers traceability from the battery pack level all the way to the cell level. This ensures that data is recorded as per the assembly requirements and integrated into the MES system.
At TEAL, we understand that battery manufacturing automation needs to be efficient, flexible, and scalable. We also know that reliability, workmanship, service support, data management, and confidentiality are important factors to consider when choosing a corporate partner. That is why we are committed to providing the best possible solution for your company’s needs.
Our commitment to quality enables us to respond quickly to customer demands and deliver orders on time. Additionally, our scalable and flexible business model allows us to easily adapt to changing market conditions. We want to help you avoid unscheduled downtime and get the most out of your equipment so you can see a significant return on your investment. Our team offers a variety of support and maintenance services that can be customized to your specific needs. We will measure key performance indicators for each stage of your production line. Afterward, we will provide you with a report detailing the expected increase in overall equipment effectiveness (OEE). Our goal is for your equipment to always meet or exceed your expectations.
TEAL’s production monitoring software is designed to increase visibility, safety, production utilization, and control through easy access to accurate data in real-time. With this production monitoring tool, we get utilization reports, comparisons, and early warnings to help you improve line efficiency by localization of bottlenecks and identifying the causes. Adding an autonomous PLC Controller to the existing or new production EV battery pack assembly line allows for a comprehensive and convenient collection of production-related information, as well as starts continuous monitoring.
We specialize in top-quality components for EV battery manufacturers and other battery production operations. With years of experience working with OEMs in the e-mobility industry, we have gathered extensive knowledge of the entire battery manufacturing process. Our expertise includes EV components and battery manufacturing applications like EV battery pack assembly, module mounting, and battery cell manufacturing. It also includes handling modules and pallet applications for manufacturing, testing, assembly, and laser marking.
Unique capabilities that distinguish TEAL from others
What sets us apart is our attention to total quality parameters and tracking that ensures safety and long battery life. We have an end-to-end operational integration, starting from cell testing, and stack formation all the way to end-of-line testing. Moreover, our SCADA system ensures customized recipe handling while our complete precaution for safety against electrostatic shocks keeps your team safe. Our Servo, Robots, Vision Systems, and Fixtures provide the accuracy and speeds you need with error-proofing to ensure safety.
In EV battery pack assembly processes, repeatable and accurate dispensing is critical in order to meet those requirements. With worldwide customers and innovation centers, our EV battery pack assembly experts provide quick and custom support for your application and design optimization needs. When it comes to an electric vehicle battery pack and module assembly applications, TEAL is your go-to source.
As the demand for electric vehicles grows, so does the need for batteries that are safe, high-performing, and lightweight. In order to meet this demand, manufacturers are constantly innovating and developing new battery technologies. This means that the future is definitely here for electric vehicles and TEAL is here to support you on this journey!