The Significance of Cell Sorting in EV Battery Technology
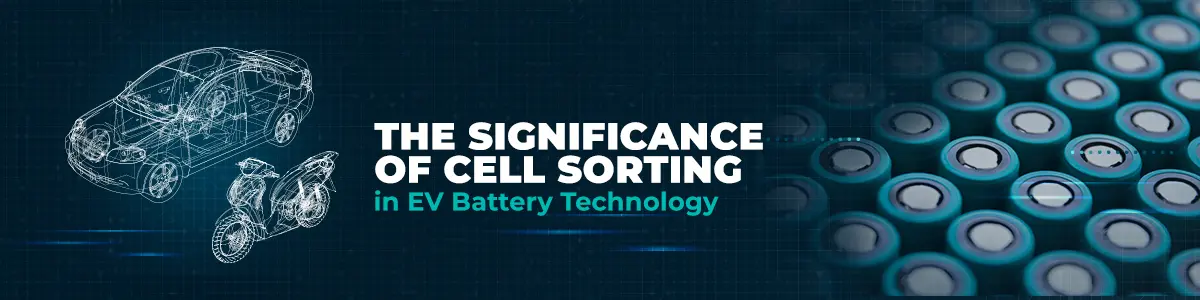
Contents
- 1 Significance of cell sorting in EV manufacturing
- 2 The Role of Cells in Electric Vehicles
- 3 What challenges do EV manufacturers face in cell sorting?
- 4 Driving Innovation with TEAL's Expertise in Cell Sorting Technology for Electric Vehicles
- 5 Revolutionizing Efficiency and Quality Control in EV Manufacturing
- 6 Driving Integration, Efficiency, and Success in EV Manufacturing with TEAL
- 7 Benefits of TEAL's Cell Sorting Solutions: Streamlined Manufacturing for Enhanced Efficiency
- 8 Enhanced Cell Quality and Performance: Maximizing EV Performance, Longevity, and Efficiency
- 9 Compliance with Industry Standards: Ensuring Quality, Safety, and Regulatory Adherence
- 10 Streamlining EV Battery Manufacturing with TEAL's Cell Sorting Solutions
- 11 Frequently Asked Questions
In the dynamic world of electric vehicles (EVs), battery technology's progress is crucial for sustainable mobility. Cell sorting, a vital process in EV battery manufacturing, greatly influences battery performance. Titan Engineering and Automation Limited(TEAL), a leader in providing assembly solutions for EV manufacturers, understand this significance and empowers manufacturers with specialized cell sorting solutions, enhancing production efficiency and battery grading as per the customer requirement.
The heart of every EV is its battery, composed of numerous cells. The quality and uniformity of these cells directly impact the vehicle's overall performance and range. Efficient cell sorting ensures batteries are made of cells with consistent characteristics, optimizing performance, extending range, and enhancing reliability. As the demand for EVs grows, streamlined processes, like TEAL's customized assembly solutions, become essential for handling large volumes of cells accurately and swiftly, elevating overall manufacturing efficiency. TEAL's cutting-edge technologies and automated systems revolutionize the battery manufacturing process, reducing errors, minimizing downtime, and driving progress in the EV industry.
Significance of cell sorting in EV manufacturing
Cell sorting plays a pivotal role in the manufacturing of electric vehicles(EVs), ensuring the efficient functioning of their vital component—the battery. This process involves categorizing individual battery cells based on characteristics such as capacity, voltage, and IR (Internal Resistance), enabling EV manufacturers to create battery packs with cells that exhibit consistent performance. The significance of cell sorting is evident as it directly influences the overall performance and reliability of EVs.
By ensuring a harmonious arrangement of cells with similar attributes, cell sorting leads to optimized energy output, increased driving range, and a smoother driving experience. Moreover, efficiency in cell sorting is crucial as it directly impacts the overall performance of EVs. Through advanced and precise sorting techniques, EV manufacturers can achieve higher accuracy levels, ensuring that each battery pack meets stringent quality standards. Improved cell sorting processes not only optimize EV performance but also contributes to sustainability by maximizing battery life and minimizing waste. As a leading provider of assembly solutions for EV manufacturers, TEAL recognizes the importance of efficient cell sorting in driving the future of sustainable mobility.
The Role of Cells in Electric Vehicles
The cells in electric vehicles, particularly lithium-ion batteries, are crucial for their functioning and performance, serving as energy storage units that determine efficiency and range. Cell quality directly impacts vehicle performance. Higher energy density and stability result in more power, enabling faster acceleration and longer travel distances.
Consistency in cell characteristics like capacity and voltage allows cells to work harmoniously, maximizing battery and vehicle efficiency. However, deviations in cell quality can lead to imbalances, reducing performance and affecting range and lifespan. Ensuring high-quality, consistent cells is essential. EV manufacturers prioritize reliable suppliers, emphasizing cell chemistry, manufacturing processes, and quality control. By focusing on cell quality, manufacturers deliver vehicles with improved acceleration, range, and reliability, with cell sorting process.
What challenges do EV manufacturers face in cell sorting?
EV manufacturers face significant challenges during cell sorting, particularly when dealing with a multitude of cells. The scale and volume of cells involved in EV production require efficient handling and sorting mechanisms. Manual sorting becomes impractical and time-consuming, necessitating the need for high-speed, automated processes to handle large volumes efficiently.
Another critical challenge that EV manufacturers face is maintaining strict quality control during the cell sorting process. Consistency in cell quality is vital to ensure optimal performance and reliability of EV batteries. Using cells of varying quality poses risks such as imbalances within the battery pack, leading to reduced performance and potential issues with the range and lifespan of the electric vehicle.
To address these challenges, EV manufacturers need advanced cell sorting technologies that can handle high volumes of cells accurately and swiftly while maintaining strict quality control standards. Automated sorting systems, coupled with robust quality control measures, ensure consistent and reliable cell sorting, leading to optimized EV performance and enhanced customer satisfaction.
Driving Innovation with TEAL's Expertise in Cell Sorting Technology for Electric Vehicles
TEAL stands as a trailblazer in the realm of cell sorting solutions, bringing forth their unparalleled expertise in designing and manufacturing assembly systems specifically catered to the needs of EV manufacturers. With a deep understanding of the intricate demands of electric vehicle production, TEAL has honed its capabilities to address the challenges posed by cell sorting with remarkable finesse.
TEAL's specialized assembly solutions are a testament to their commitment to excellence. These solutions are meticulously crafted to seamlessly integrate into the existing production lines of EV manufacturers. By doing so, TEAL ensures a smooth and efficient adoption of their cutting-edge technologies without disrupting the overall manufacturing process. This seamless integration optimizes production efficiency, reduces downtime, and streamlines the entire cell sorting operation.
TEAL's dedication to delivering state-of-the-art assembly systems that effortlessly mesh with existing infrastructures not only showcases their technical prowess but also underscores their unwavering commitment to supporting EV manufacturers on their journey towards producing sustainable and high-performance electric vehicles.
Revolutionizing Efficiency and Quality Control in EV Manufacturing
TEAL takes pride in its ability to develop customized cell sorting equipment tailored to meet the unique requirements of EV manufacturers. By closely collaborating with clients, TEAL understands their specific needs and incorporates cutting-edge technologies into its solutions.
One of the key features of TEAL's customized cell sorting equipment is its versatility. TEAL's automated sorting systems revolutionize cell sorting for EV manufacturers, offering a multitude of advantages. Speed is a critical factor in manufacturing, and TEAL's solutions excel in this aspect, enabling manufacturers to meet market demands efficiently by significantly reducing production time. Moreover, TEAL's advanced algorithms and sensor technologies ensure exceptional cell classification and organization accuracy. This precision enhances the uniformity and consistency of battery packs, optimizing their overall performance.
With a strong focus on quality control, TEAL implements rigorous measures, including real-time monitoring though advance traceability and data analysis, to select only the highest-quality cells for integration into battery packs. This commitment not only improves battery performance and longevity but also minimizes the risk of defects and malfunctions. TEAL's expertise in developing customized cell sorting equipment, combined with the advantages of its automated sorting systems in terms of speed, accuracy, and quality control, empowers EV manufacturers to enhance their production efficiency and deliver high-quality, reliable batteries for electric vehicles.
Driving Integration, Efficiency, and Success in EV Manufacturing with TEAL
TEAL stands out for its commitment to fostering a collaborative partnership with EV manufacturers, working closely to understand their unique needs and challenges. Through open communication and active engagement, TEAL gains a comprehensive understanding of the manufacturer's requirements, enabling the development of customized solutions that precisely align with their objectives. This collaborative approach ensures seamless integration of TEAL's assembly systems and cell sorting solutions into existing production lines, minimizing disruptions and maximizing efficiency.
With TEAL's experts will work with you to provide guidance, technical support, and training. This partnership enables successful implementation, ongoing optimization, and continuous improvement of cell sorting processes. The result is enhanced integration, efficiency, and long-term success for EV manufacturers, solidifying TEAL's position as a trusted partner driving sustainable and high-performance electric vehicles in the industry.
Benefits of TEAL's Cell Sorting Solutions: Streamlined Manufacturing for Enhanced Efficiency
TEAL's advanced cell sorting solutions offer EV manufacturers a multitude of benefits, particularly in terms of improved production efficiency. By automating the sorting process with advanced algorithms and sensor technologies, TEAL ensures precise classification and organization of cells, eliminating the need for manual sorting and reducing human error. As a result, manufacturers experience streamlined manufacturing processes, leading to significant reductions in time and labor costs.
The impact of increased production efficiency is far-reaching. Manufacturers can maximize output without compromising on quality, responding promptly to market demands with shorter production cycles. This heightened agility enhances competitiveness and meets customer expectations in the fast-paced EV industry. Furthermore, improved production efficiency directly influences cost savings, allowing manufacturers to allocate resources more effectively and drive profitability. The savings achieved can be reinvested in research and development, fueling innovation and propelling growth in the EV market.
TEAL's cell sorting solutions usher in a transformative shift, empowering manufacturers to streamline processes, reduce time and labor costs, and effectively meet market demands. By embracing these solutions, EV manufacturers can secure their position at the forefront of the industry, delivering high-quality electric vehicles efficiently and staying ahead of the competition.
Enhanced Cell Quality and Performance: Maximizing EV Performance, Longevity, and Efficiency
TEAL's advanced cell sorting processes like OCV(Open circuit voltage), IR(Internal Resistance), Polarity checking, and traceability play a crucial role in maintaining consistent cell quality, directly impacting the performance and longevity of electric vehicles(EVs). By implementing TEAL's solutions, manufacturers can ensure that each battery pack comprises cells of the highest quality and uniformity.
TEAL's systems employ rigorous quality control measures, including real-time monitoring and data analysis, throughout the cell sorting process. This ensures the selection of reliable and high-quality cells, resulting in improved acceleration, extended driving range, and a more efficient driving experience for EV owners. These cells deliver optimal energy output, enhancing the overall efficiency of the vehicle and enabling drivers to travel longer distances on a single charge.
Using reliable and high-quality cells in EV production offers additional benefits, including improved fuel economy and optimized range. These cells are less prone to degradation, contributing to the longevity of the EV's battery and maintaining its performance and capacity over time. By integrating TEAL's cell sorting solutions, manufacturers can deliver electric vehicles that excel in both performance and longevity.
Compliance with Industry Standards: Ensuring Quality, Safety, and Regulatory Adherence
TEAL prioritizes adherence to industry standards and regulations in the development of cell sorting equipment. By following these stringent requirements, TEAL's solutions meet the highest industry benchmarks, ensuring the quality, safety, and regulatory compliance of the sorting equipment. This commitment to compliance instills confidence in EV manufacturers, assuring them of TEAL's dedication to delivering reliable and high-performance solutions.
TEAL's dedication to maintaining consistent cell quality and adherence to industry standards in cell sorting equipment development reinforces its commitment to delivering high-performance, reliable, and compliant solutions to the EV industry. Manufacturers can confidently meet stringent quality and regulatory requirements by leveraging TEAL's expertise and solutions, producing electric vehicles that excel in performance, longevity, efficiency, and safety. With TEAL as their trusted partner, EV manufacturers can navigate the complex landscape of industry standards and deliver cutting-edge EVs that meet the highest safety and quality standards, propelling the industry towards a sustainable and efficient future.
Streamlining EV Battery Manufacturing with TEAL's Cell Sorting Solutions
In the ever-evolving landscape of electric vehicles (EVs), staying abreast of the growing demands for advanced battery technology is paramount. Meeting these demands and further enhancing the performance and lifespan of EV batteries relies on a pivotal process known as cell sorting. In this blog we discussed the challenges faced by EV manufacturers to benefits of cell sorting and how TEAL's assembly solutions is paving the way ahead in this industry.
TEAL's expertise in designing and manufacturing assembly systems for EV manufacturers ensures seamless integration into existing production lines. Our customized cell sorting equipment caters to the unique requirements of each client, offering advantages such as speed, accuracy, and quality control. With TEAL's automated sorting systems, manufacturers can streamline their processes, reduce time and labour costs, and meet market demands more efficiently.
If you are interested in learning more about TEAL's cell sorting solutions or discussing your specific requirements in EV assembly and cell sorting, we invite you to reach out to us. Together, we can make a significant impact on the future of electric mobility, driving towards a more sustainable and environmentally friendly world.
Frequently Asked Questions
In EV battery technology, there are three main types of cell sorting techniques commonly used:
Manual Sorting: This method manually inspects and categorizes battery cells based on their specific characteristics. It requires human intervention and can be time-consuming and prone to human error. Manual sorting is typically used for smaller-scale operations or in situations where automation is not feasible.
Automated Sorting: Automated sorting utilizes advanced technology, such as sensors, algorithms, and robotic systems, to classify and organize battery cells based on predetermined criteria. This method offers higher accuracy, speed, and efficiency compared to manual sorting. Automated sorting is suitable for large-scale production, where a high volume of cells needs to be processed quickly and accurately.
Optical Sorting: Optical sorting utilizes optical sensors and imaging technology to analyze and sort battery cells based on visual characteristics. This technique involves capturing images of the cells and using algorithms to identify specific attributes such as size, shape, color, and defects. Optical sorting offers precise and reliable sorting results, particularly for cells with visually distinguishable characteristics.
Each type of sorting method has its own advantages and considerations, depending on the scale of production, desired accuracy, and specific requirements of EV manufacturers. The choice of sorting method depends on factors such as production volume, cost-effectiveness, and the need for consistency and quality control in the battery manufacturing process.
Cell sorting is a critical process in EV battery technology, serving several important purposes. Firstly, it optimizes the performance of electric vehicle batteries by grouping cells with similar attributes, such as capacity, voltage, and internal resistance(IR). This ensures consistent performance, improves overall battery efficiency, and extends the driving range of electric vehicles. Secondly, cell sorting enables effective quality control by identifying and eliminating cells that do not meet the required standards. By selecting high-quality cells, manufacturers can enhance the battery's reliability, safety, and longevity.
Furthermore, cell sorting facilitates the balancing and uniformity of battery packs, ensuring an even distribution of cells and preventing issues such as overcharging or undercharging. This balance enhances the efficiency and lifespan of the battery. Lastly, cell sorting contributes to the consistency and reliability of electric vehicles. By implementing stringent cell sorting processes, manufacturers can deliver electric vehicles that perform consistently across different units, meeting the expectations of customers. Overall, cell sorting is essential in EV battery technology to optimize performance, maintain quality control, achieve balanced battery packs, and deliver reliable electric vehicles to the market.