Industrial Automation’s potential to transform manufacturing
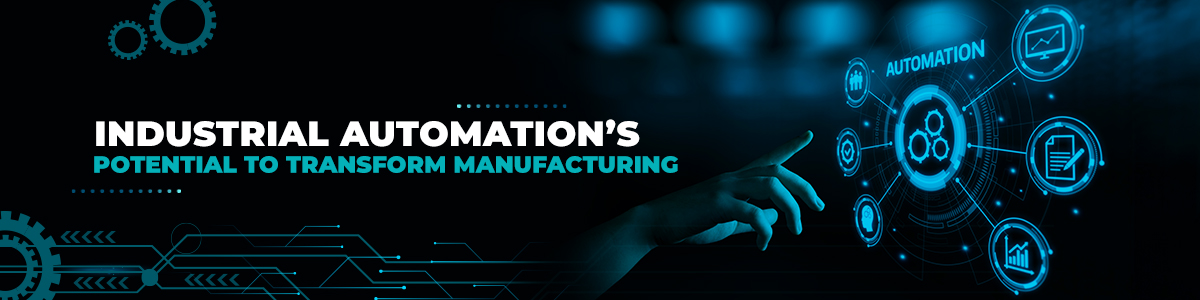
The raft of new technologies, most of which are centered on Artificial Intelligence (AI), Machine Learning (ML), or digital transformation, that have become available to the manufacturing sector holds the promise of not merely enhancing their performance but accelerating their growth. In its report on ‘Digital Factories’, PwC pointed out that accelerating the pace of ‘Digitization’ could place Indian manufacturers in a position where they could look to increase their production, and even pip their global competitors (EY report).
So, why should companies either invest or, if they have already adopted Industrial Automation, increase their outlay towards it? Read on to find out.
Why Automation?
Statista estimated that, as of 2023, there were more than 15 billion Internet of Things (IoT) devices in use the world over, rising by more than one billion from the previous year. The sheer ubiquity of IoT devices, the use of which is no longer confined to the assembly line of a manufacturing plant, is largely the result of rising awareness among stakeholders of industry, across sectors, of the manifold benefits that they can accrue from their use (Statista report). The rise in the number of IoT devices has been accompanied by a proportional increase in the outlay for 5G technology. In India, this is particularly the case, with the year-on-year (YoY) expenditure on IoT and 5G registering a 4% increase. Notwithstanding the relatively sluggish pace at which the Indian manufacturing firms are embracing digitization – nearly 38% of the firms that responded to PwC said that there were no plans to integrate digital solutions into their operational set-up in the pipeline (PwC report) – there is much optimism, coupled with undisguised excitement among stakeholders of Indian industry over the scope of possibilities that automation-powered digital transformation can open up for them.
The uptick in efficiency that automation and AI-powered processes guarantee is one of the biggest reasons why even those companies yet to plan, or map, their digital transformation journeys, are hedging their bets on automation. The rise in the number of IoT devices also attests to the very feasible goal of an autonomous assembly line wherein an entire cohort of devices, communicating and coordinating with each other, is working in tandem with human resources. Experts have been emphasizing that, in the years to come, manufacturing will revolve primarily around creative collaboration between robots and human beings.
More than any other function, maintenance is tending increasingly towards automation. The ability of automated systems to run periodic diagnostic checks and identify technical glitches through highly advanced simulation tests has enabled manufacturing firms to adopt a proactive instead of a reactive approach to maintenance. ‘Intelligent Instrumentation’ has, in fact, enabled machines to achieve near-complete independence when it comes to maintenance.
Precision, reduced costs driving widespread adoption in India
Several Indian firms, having identified the benefits of automation, have taken to automation, and its potential for transformation, wholeheartedly. For tasks that require precision, particularly at microscopic scales, use of automation solutions ensures not merely efficiency and consistency regardless of the number of times the task is to be repeated, but also accuracy. For instance, at food-and-beverage plants, use of automated tools can ensure zero wastage or spillage of respectively the food product or the liquid that is to be packed into either a pre-determined plastic packet or a small bottle. Similarly, many pharmaceutical firms in India have, in acknowledgement of the benefits of automation in processes that involve the handling of reactive chemical substances, replaced human labor with robots. Given the need for a sterile environment for the manufacture of medicines, minimizing the presence of human presence on the floor greatly reduces the risk of transmission of infectious diseases. Furthermore, given that many of the chemicals used in the manufacture of drugs could lead to illness among people coming directly in contact with the same, substituting human workers with robots could not only limit exposure of humans to hazardous chemicals but also make the entire function a lot safer.
Automated assembly lines, which are a specialized area of expertise for TEAL, are in high demand across sectors, ranging from automotive and pharmaceutical to the Electric Vehicle (EV) industry. As the world moves towards electric vehicles and a sustainable future, automation plays a crucial role in enhancing efficiency, reducing waste, and supporting the growing need for eco-friendly manufacturing solutions.
Automation systems are essentially highly well-connected networks of cutting-edge electronic devices, each working in tandem, and simultaneously with each other. But what exactly are these systems, and how do they ensure seamless operations of such advanced technologies?
Key components and technologies
At the heart of any Industrial Automation system is an array of control systems, each working in consort with one another. The functioning of most of these control systems is governed by devices that fulfil a very specific function, operating, in their very limited capacity, like computers; these are called Programmable Logic Controllers (PLCs). From activating specific parts of a larger circuit – in this avatar, a PLC is little more than a switch – to relaying signals throughout the system to ensure perfect co-ordination across different and disparate functional arms of a larger automation device, a highly complex network of PLCs oversees operations, large and small. Advancements in automation technology, therefore, primarily entails boosting the capabilities of the PLCs. These devices also play a key role in relaying feedback collected on a wide array of parameters – quality, efficiency, et al – to subsequent systems in the production line, which act as inputs, enabling autonomous devices to voluntarily adopt corrective measures to boost overall productive efficiency.
Equally vital to ensuring seamless operations in an automated network is the Supervisory Control and Data Acquisition (SCADA) system. Unlike the PLC that relies extensively on feedback, and functions, effectively, as a closed loop system, SCADA’s function is based on an open-look framework. Owing to the fact that SCADA systems are open-loop, their functional scope is not constrained by space or geographical boundaries. Their functional or supervisory scope can span different geographical locations, while ensuring each functional node is operating in sync with each other.
At TEAL, we provide automation solutions for a wide range of industries, including energy, life sciences, among others. Our solutions are tailored to meet the specific requirements of energy companies, telecom operators, among others, to enable them to reduce their consumption of energy.
As an enterprise committed to expanding our suite of innovative solutions, and our operational scope, TEAL is also exploring the many possibilities that the use of the ‘Digital Twin’ can unveil. A virtual replica of a physical system, the ‘Digital Twin’ has been around for more than six decades, and in the wake of recent advancements in the use of ‘Smart’ technologies such as IoT devices, and smart sensors, the potential for its application has increased vastly.
Benefits notwithstanding, why is adoption slow?
What is throttling automation from simply taking off? The benefits that industries are likely to accrue from the integration of Industrial Automation are many, not to mention the obvious impact it will have on their bottom line in the long-run. What then explains, at least in India, the reluctance to embrace Industrial Automation.
To start with, the capital expenditure involved in the adoption of automation systems, coupled with the challenges involved in integrating them with existing assembly lines, is a hurdle to embracing automation. In 2022, McKinsey estimated that automation would account for 25% of the capital expenditure across sectors in the industrial landscape over the next five years (McKinsey report). Even sectors not particularly labor-intensive such as retail were planning on increasing expenditure on retail, with plans to allocate sums as vast as USD 500 million. However, reservations persist among Indian firms over investing such vast sums, particularly owing to the uncertainty prevalent in the global market, and no guarantee of Return on Investment (ROI). The other big hurdle to the integration of automation solutions in Indian firms is the skill gap among Indian workers. Moreover, notwithstanding India’s redoubtable digital infrastructure, ensuring speedy network connectivity remains a challenge. For companies to optimize profits from Industrial Automation systems, it is imperative that they have high-speed internet connectivity, the lack of which could severely constrain their efficiency.
Use of data to drive efficiency of automated systems
Although the idea of Big Data tools and Industrial Automation systems working in tandem, and even complementing each other’s functions may sound, at first, slightly fantastic, combining the capabilities of two advanced technologies could effectively double the benefits of automation itself. Although the use of Big Data has hitherto been seen as being the preserve of consumer-centric businesses, their possible application on the assembly line of a manufacturing firm can have a similarly transformative impact.
The best example of the use of Big Data tools in an automated system would be the system’s integration with the machinery’s maintenance mechanism. A Big Data tool, equipped with information on the parameters used to provide a comprehensive picture of a machine’s health, would be better able to detect a glitch in the event of the slightest deviation from standard measurements. Similarly, the use of data-driven decision making could enable companies to run better simulations to more accurately measure the production capabilities of their automated plants.
Rest assured; robots will not replace human workers. In fact, robots will probably drive employment; but it is vital that prospective employees boast the requisite skillset. Read on to know if automation can create jobs.
Automation is the future – Do you see yourself in it?
Notwithstanding the numerous studies published by reputed consulting firms the world over, the fear of AI and robots driving people out of jobs persists among large sections of the global populace. However, automation and robots, far from driving employees in their thousands out of jobs, are likely to create many more. The World Economic Forum (WEF), no less, estimates that ‘Smart Manufacturing’ or automation-powered manufacturing can create anywhere between three million and six million jobs across the globe (WEF Report).
Little wonder then that engineers, as they are today, will continue to be in demand even a decade down the line. But the key challenge for engineers – electrical, software, mechanical and electronics engineers – will be to stay abreast of the latest advancements in automation and make themselves not merely attractive in the rapidly changing industrial landscape, but indispensable assets. Designing, coding, maintaining, and supervising robots, will require human intervention. Furthermore, Industry 5.0, when it comes, will be characterized by increased and efficient collaboration between humans and robots. Engineers and technicians will have to work towards acquiring niche skills, besides taking care to avoid being pigeonholed into specific roles. While specialization is good, it cannot be pursued to the exclusion of all else. For instance, experts in automation will ignore the potential that Big Data offers for growth at their own peril.
A promising future
Estimates peg the value of the automation market to rise to USD 218 billion in three years, while there is speculation of the figure crossing the USD 300 billio0mark by 2030 (Markets&Markets). Even companies have yet to invest in digitization and automation as today are exploring opportunities to integrate these tools into their systems to reap the dividends of increased efficiency and productivity. With advanced systems powered by edge computing technology already finding increased application across sectors, a near-complete autonomous manufacturing plant where an entire network of smart sensors and devices are operating in perfect harmony with each other no longer seems as far-fetched.
From unmanned mining vehicles that can accurately map the labyrinthine passages of the cavernous mines, and accordingly decide the journey to be taken, to digital maturity systems that can, independently assess the extent of digitization of their operational network, the possibilities for automation are immense. Advancements in automation will save humans from having to be deployed in a slew of dangerous jobs, such as mining, besides freeing invaluable resources from repetitive tasks, thereby enabling companies to more fully utilize their workforce, extracting the most out of them without driving them to physical or mental fatigue.
Frequently Asked Questions