Challenges & opportunities in using Industry 4.0 solutions
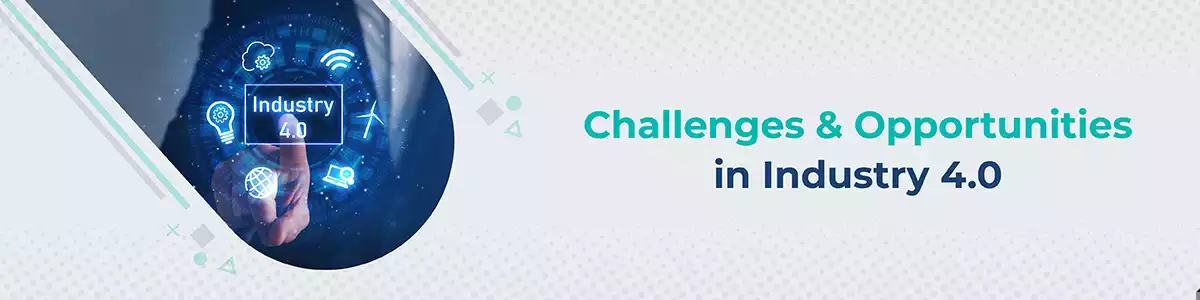
Contents
- 1 For companies who want to stay competitive, adopting Industry 4.0 solutions is crucial
- 1.1 How to start
- 1.2 Using legacy systems
- 1.3 Lack of domain expertise
- 1.4 Estimating the ROI
- 1.5 Finding the right fit
- 1.6 Diversity of machines
- 1.7 Infrastructure
- 1.8 Robust testing of solutions
- 1.9Incorporating new technology into existing infrastructure
- 1.10 Attrition and attraction towards work from home
- 2 Incorporating Industry 4.0 solutions into your operations can have many benefits
- 3 Frequently Asked Questions
The digital age and Industry 4.0 are transforming the manufacturing industry. The fourth industrial revolution brings innovative technologies like the Internet of Things, robotics, and augmented and virtual reality, streamlining the manufacturing process and making it more automated and efficient. Algorithms and machine learning are also playing a crucial role in making manufacturing models smarter and capable of operating on their own. This marks a departure from traditional manufacturing practices and signals a new era in the industry. According to a recent report by the World Economic Forum, an impressive 70% of manufacturers have embraced Industry 4.0 solutions and are automating their operations.
For companies who want to stay competitive, adopting Industry 4.0 solutions is crucial
Automation plays a significant role in Industry 4.0, enabling companies to leverage their power for better intelligence and decision-making. However, it comes with its risks and challenges as the digital and real worlds become interconnected through cyber-physical systems. Improper integrations can lead to malfunctions and damage to facilities, products, and workers. The increase in network-connected devices also makes companies more vulnerable to cyber-attacks, compromising the system's security. Other challenges in Industry 4.0 adoption include connectivity, visibility, the skills gap, and compatibility with legacy equipment.
Implementing Industry 4.0 solutions is subject to variability across companies, depending on factors such as awareness, capabilities, and financial resources. In our organization, Titan Engineering and Automation Limited (TEAL), we encountered certain obstacles but overcame significant hurdles. This blog outlines the foremost challenges we faced while embracing Industry 4.0. Our first challenge was how to get started.
How to start:
The implementation of Industry 4.0 solutions can revolutionize the way processes are carried out. Still, it can also be daunting and confusing, especially for new manufacturers embarking on their Industry 4.0 journey. Determining which areas to prioritize can be complex, such as material management and cost savings, tool and inventory management, or quality control and process optimization.
To tackle this challenge, we started by pinpointing the most crucial areas in our business that were underperforming. Rather than trying to solve multiple problems simultaneously, we focused on addressing a single significant issue first and gradually expanded our solutions to other areas. This approach allowed us to start small, succeed quickly, and grow further.
The manufacturing industry has long relied on various legacy data systems. As the industry moves towards Industry 4.0 and its accompanying automation, manufacturers face the challenge of integrating new data systems with existing databases. Solution providers must consider this when designing Industry 4.0 solutions to ensure seamless integration and avoid costly investments in new tools and time-consuming data transfers.
Initially, our customers experienced delays due to outdated systems. To solve this issue, we started adopting Industry 4.0 solutions, which led to a significant increase in efficiency—10X more than before—and eliminated delays.
Lack of domain expertise:
Having domain expertise means that engineers know and understand KPIs in production. Recently, we recognized a need for more awareness among our team. While skilled in creating software, such as charts, graphs, and pop-ups, they need help to grasp the data's authenticity fully. We have since addressed this issue and are working to improve their understanding of the end-to-end process involving Industry 4.0 solutions.
Estimating the ROI:
It is natural for manufacturers to seek a reasonable forecast of their potential investment returns. They aim to grasp the same business benefits from integrating Industry 4.0 solutions. Nonetheless, calculating the ROI for Industry 4.0 solutions is a challenging task.
To accurately gauge the impact of technology, we assessed its potential to improve efficiency, productivity, quality control, and employee performance. Therefore, manufacturers must choose solution providers that offer precise estimations of the actual benefits their solutions can deliver.
Finding the right fit:
A wide variety of Industry 4.0 solutions are available on the market, but it's essential to recognize that not all of them may be the best fit for addressing your business concerns. Every manufacturer has distinct requirements, and the obstacles they encounter will also be unique. As a result, selecting a solution that is a perfect match for your business objectives is crucial.
Before choosing Industry 4.0 solutions, we dedicated much time to thoroughly evaluating numerous options. Our approach involved comprehending our customers' business requirements and searching for solutions that meet those needs. This enabled us to prevent significant expenses, reinvestments, and losses.
Diversity of machines:
Each machine presents its unique set of challenges, making it difficult to ensure that our software is compatible with them. This requires a deep understanding of each machine's specific characteristics and capabilities and the ability to adapt our software to meet the requirements. Additionally, this also requires a level of flexibility and adaptability on our part, as we may need to modify our software as new machines are developed and introduced to the market.
Infrastructure:
As organizations adopt Industry 4.0 solutions, infrastructure can present challenges and opportunities. One major challenge is the need for additional resources, such as computational power and more robust hardware, to support the new technologies. To overcome this challenge, we sought assistance from software providers, which made changes to our architecture and established training programs to enhance the expertise of our staff. We have also embraced cloud technology to create a scalable, reliable, and secure platform to handle multiple machine data and users simultaneously. By addressing infrastructure challenges in this way, organizations can take advantage of the opportunities presented by Industry 4.0 solutions and reap the benefits of increased efficiency, productivity, and innovation.
Robust testing of solutions:
To overcome the challenges in adopting Industry 4.0 solutions, robust testing is essential. TEAL recognizes the importance of testing and has taken steps to develop a machine simulator. This simulator is designed to mimic the behavior of shopfloor machines, generating alarms and rejections to simulate real-world scenarios. Additionally, TEAL is working on incorporating a visual component into the simulator, which will allow visitors to see the machines in action. TEAL aims to ensure that Industry 4.0 solutions are reliable, effective, and practical for businesses to adopt by investing in such testing solutions.
Incorporating new technology into existing infrastructure:
Although creating a new, unified system is often more accessible, it may not be feasible. When retrofitting a factory with Industry 4.0 solutions, it is essential to consider crucial factors such as connectivity, network reliability, and cybersecurity, which become even more vital as the factory becomes more connected. Additionally, acquiring or contracting the necessary skills to implement the technology correctly, including forecasting network usage and data processing needs, is crucial.
Attrition and attraction towards work from home:
In today's highly competitive job market, employees are always on the lookout for better pay and career growth opportunities. When they come across a company that offers higher salaries and more opportunities for advancement, they may decide to leave their current company and join the new one.
The option of working from home has become essential for many people. When we interview candidates, around four out of ten express a preference for working from home. However, this is only sometimes an option that the company can afford. As the job market becomes increasingly competitive, we have found recruiting employees willing to work on-site challenging. To address this challenge, we have started being more specific about the nature of the job during the recruiting process, ensuring that candidates understand that they may need to travel for work.
Although not exhaustive, the list above aims to caution manufacturers about the main obstacles they may encounter while adopting Industry 4.0. The dynamic and rapid nature of Industry 4.0 technologies suggests that this list of challenges will keep evolving. As a result, businesses must adequately prepare themselves before venturing into this journey, knowing that each obstacle has a solution. To address the challenges, TEAL highlights several benefits of implementing Industry 4.0 to enhance the manufacturing process. Here are some of them.
Incorporating Industry 4.0 solutions into your operations can have many benefits
Industry 4.0 solutions streamline operations, improve efficiency, and enhance overall productivity. Incorporating these solutions into your operations can have numerous benefits to help your business grow and thrive.
One of the primary benefits of Industry 4.0 solutions is increased efficiency. Advanced technologies can automate many repetitive, manual tasks that would otherwise require human intervention, freeing up resources and allowing for greater output with fewer errors. For example, using robotics to automate assembly line processes can significantly reduce production time and costs.
Another benefit of Industry 4.0 solutions is improved quality control. With the use of sensors and other advanced technologies, businesses can track and monitor products in real-time, allowing them to identify any potential issues before they become significant problems. This can lead to better quality control, improved customer satisfaction, and reduced waste.
Industry 4.0 solutions can also help businesses become more agile and responsive to changing market conditions. By leveraging real-time data and analytics, companies can quickly adapt their operations to meet changing customer demands and stay ahead of the competition.
Finally, Industry 4.0 solutions can help businesses reduce their environmental footprint. For example, advanced sensors and analytics can help companies identify areas to reduce energy consumption and waste, leading to cost savings and a smaller environmental impact.
Industry 4.0 is revolutionizing the manufacturing industry by allowing for the development of smart factories that are more agile, adaptable, and efficient. As businesses evolve in the digital age, adopting these technologies is becoming increasingly essential to remain competitive and achieve long-term success. By incorporating Industry 4.0 solutions into automation processes, factories can enhance their competitiveness and better cater to the changing demands of their clients. Although automation in Industry 4.0 offers many benefits, businesses may face specific challenges. TEAL can provide exceptional solutions to your business challenges if you seek to optimize your operations. Get in touch with us now!